How Glue Sticks Are Made: A Comprehensive Guide to the Manufacturing Process
Mixing the adhesive recipe in large vats is the first step in making a glue stick. The recipe usually consists of polyvinyl acetate (PVA) blended with several other materials, including water, glycerin, or coloring for colored glue sticks. Wax, specifically ethylene-vinyl wax (EVA), is also added to the mixture.
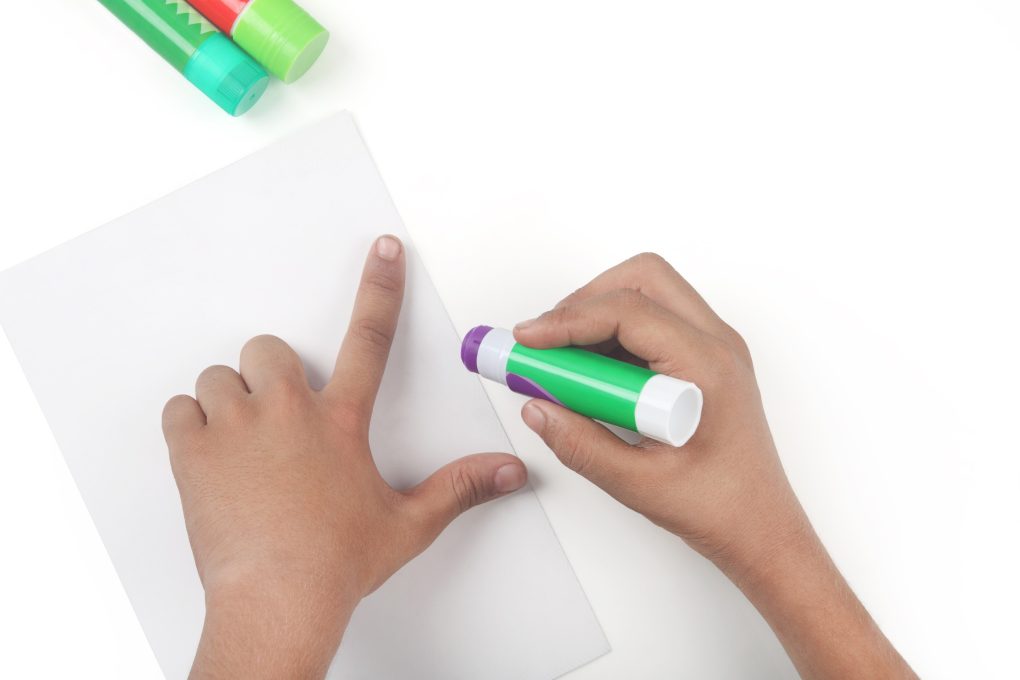
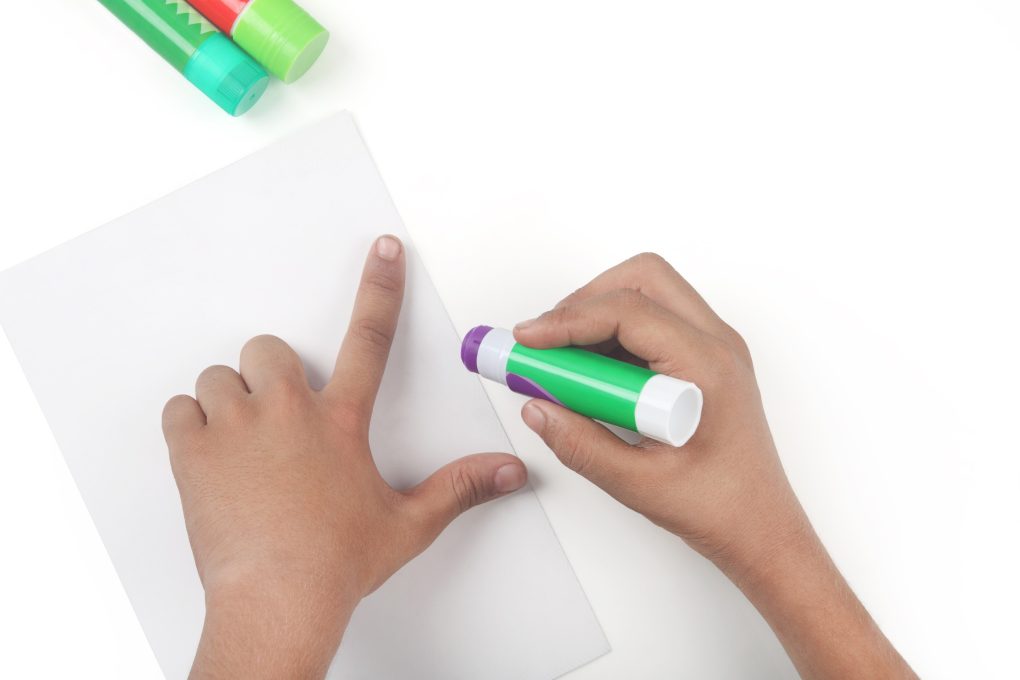
The mixture is then heated to form a liquid, which is poured into molds to create the glue sticks. Once the glue sticks have been molded, they are left to cool and harden. They are then wrapped in a protective covering and packaged using specialized machines. The result is a solid and hard adhesive that can be applied by holding the open tube to keep fingers clean and rubbing the exposed stick against a surface.
A Glimpse Into Glue Stick Making
Raw Materials
The raw materials used in producing glue sticks are carefully selected to ensure the final product is high quality. The main raw material used to produce glue sticks is polyvinyl acetate (PVA), a synthetic polymer widely used in the adhesive industry. PVA is a versatile and strong adhesive ideal for glue stick use.
In addition to PVA, other substances are added to the raw materials to create the final product and improve its performance. These include:
- Water dilutes the PVA and other chemicals to the desired consistency.
- Solvents: Used to dissolve the PVA and other chemicals to create a homogenous mixture.
- Glycerin: Used to give the glue stick a smooth and easy-to-apply texture.
- Coloring: Used to give the glue stick a specific color, such as white or clear.
- Wax: Used to improve the adhesion and prevent the glue from drying out too quickly.
- Stabilizers: Used to prevent the glue from breaking down over time.
- Anti-foaming agents: Used to prevent the formation of bubbles in the glue.
By carefully selecting and combining these raw materials, chemicals, and additives, manufacturers can create high-quality glue sticks that are easy to use and provide strong adhesion.
Manufacturing Process
In my experience, the manufacturing process for glue sticks is highly automated and relies on advanced machinery to produce high-quality glue sticks efficiently and consistently. The first step in manufacturing glue sticks is mixing the adhesive recipe.
This is done in large vats where the ingredients are combined and heated until they reach the desired consistency. The adhesive recipe typically includes a combination of polymers, resins, and other additives that give the glue unique properties.
Once the adhesive recipe is mixed, it is fed into an extruder. An extruder is a machine that heats and melts the adhesive mixture and then forces it through a die to form a continuous tube of glue. The die’s size and shape determine the glue stick’s size and shape.
After the glue has been extruded, it is cooled to solidify the adhesive. This is typically done using a cooling conveyor, where the glue sticks are placed on a moving belt and cooled by blowing air over them. Cooling is critical to ensure the glue sticks maintain their shape and consistency.
Once the glue sticks have been cooled and solidified, they are cut to the desired length. This is typically done using a cutting machine that cuts the glue sticks to the correct length and then packages them for distribution.
Quality Control and Inspection
Proper quality control measures ensure that each glue stick is consistent and meets safety standards. Quality control is performed at various stages of the manufacturing process, including testing and inspection.
Testing is done to ensure that the glue stick meets the required specifications. The glue sticks are tested for various properties, including viscosity, strength, and adhesion. The viscosity of the glue is tested to ensure that it is not too thick or too thin. The strength of the glue is tested to ensure that it can hold materials together. The adhesion of the glue is tested to ensure that it can stick to different surfaces.
The testing process involves using various instruments and equipment. For example, a viscometer is used to measure the viscosity of the glue. A tensile strength tester is used to measure the strength of the glue. An adhesion tester is used to measure the adhesion of the glue.
An inspection ensures the glue stick is defect-free and meets safety standards. The inspection involves checking the glue sticks for various defects, such as cracks, air bubbles, and discoloration. The glue sticks are also inspected to ensure they are free from harmful chemicals and meet safety standards.
The inspection process involves visual inspection and various instruments and equipment. For example, a microscope is used to inspect the glue sticks for defects. A chemical analyzer is used to test the glue for harmful chemicals.
Packaging and Distribution
Once the glue sticks have been manufactured and quality checked, they are moved to the packaging stage. Glue sticks are typically packaged in cardboard boxes or plastic bags. The packaging is designed to protect the glue sticks during shipping and to make it easy for consumers to use and store the product.
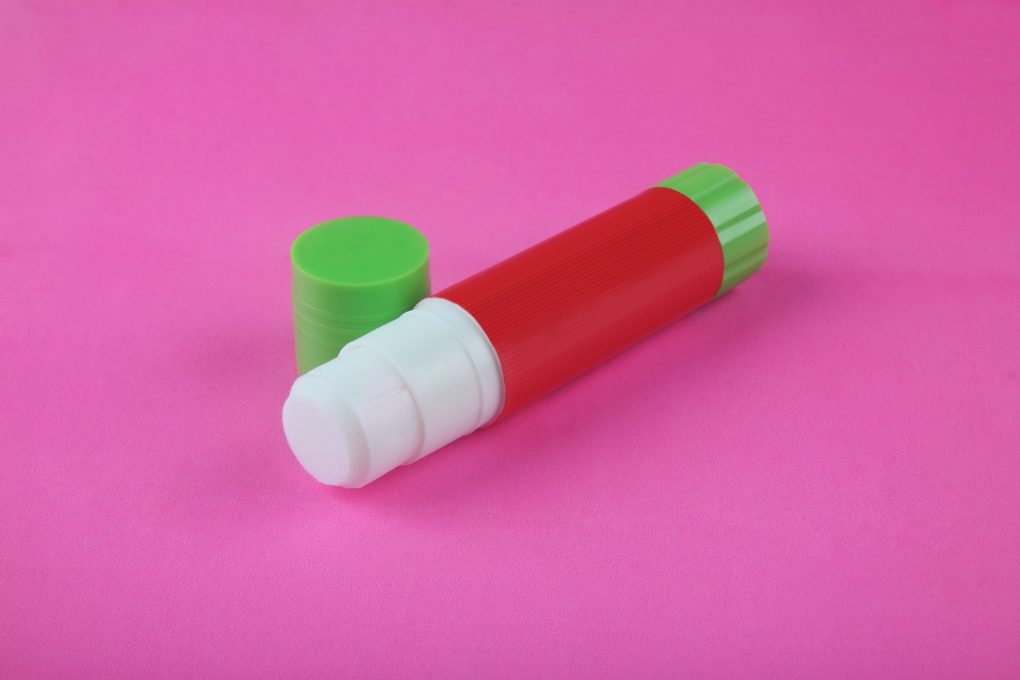
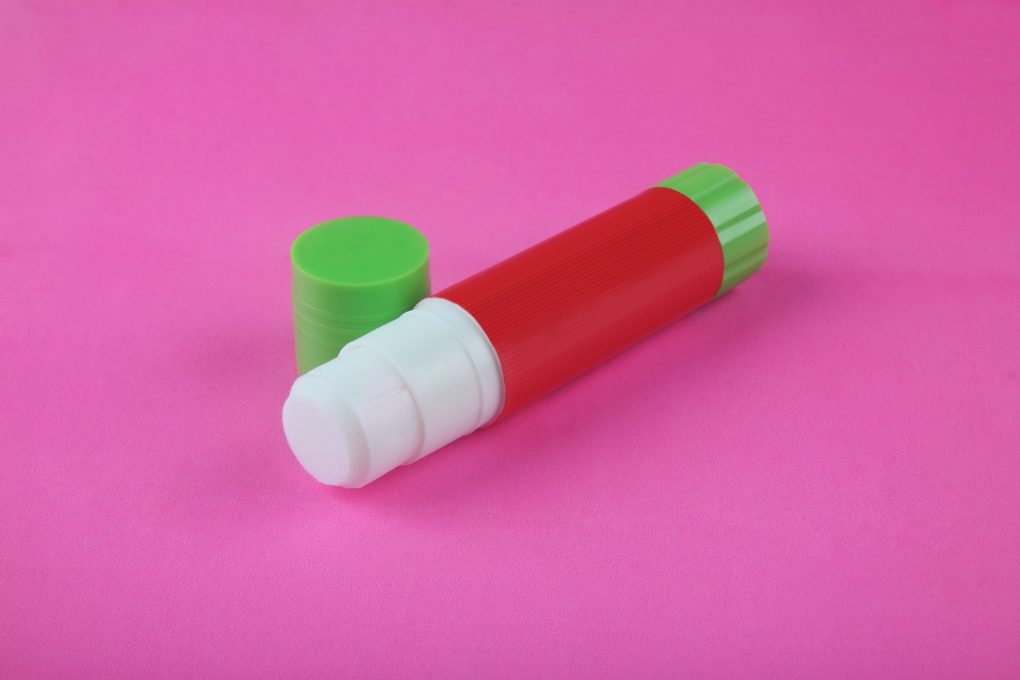
Glue sticks are best stored in a cool, dry place. Extreme temperatures can cause the glue to melt or become brittle, affecting the adhesive’s quality. Once packaged, glue sticks are shipped to retailers and distributors worldwide. Shipping methods vary depending on the destination and the number of glue sticks shipped.
For example, small quantities may be shipped via postal service, while larger quantities may be shipped via truck or cargo plane. During shipping, it is important to ensure that the glue sticks are not exposed to extreme temperatures or humidity, which can damage the product. Additionally, shipping containers should be properly labeled and secured to prevent damage during transit.